Grind Your Welds With Pride, If That’s The Way You Do It
![]() |
I had a lot of fun creating these awful welds for this piece. Mostly they are the result of too long an arc length. |
To grind or not to grind, What a question! It all depends on what you’re really trying to show, and in the case of welded joints, I often want to prove the integrity of the weld.
My ground-back piece of welded tube. Eagle-eyed readers will spot that the grinding reveals a weld that isn’t perfect.
Recently, I wrote a piece in which I talked about my cheap inverter welder and others like it. As part of it, I did a lower-current weld on a piece of thin tube and before snapping a picture of the weld I ground it back flat. It turns out that some people prefer to see a picture of the weld bead instead — the neatness of the external appearance of the weld — to allow judgment on its quality. Oddly I believe the exact opposite, that the quality of my weld can only be judged by a closer look inside it, and it’s this point I’d like to explore.
What Lies Beneath
A weld is a balance of several different factors to use an arc to melt a steel filler into the gap between two pieces of steel, shielded from oxidation by some kind of non-reactive cover. In the case of my stick welder, the cover is the molten and gaseous phases of the flux covering the welding rod as they are heated by the arc, while in the case of a MIG welder it is whatever shield gas the operator is using. As the operator, I have control of a few factors such as the current setting on the welder, the size of the arc I draw, and the speed at which I move it across the metal. These affect the temperature and thickness of the molten metal and the integrity of the shield, which will, in turn, affect the metallurgy of the resulting weld. It may be brittle, it may have inclusions of flux, it may have internal tensions that could cause cracks, or it may not have proper adhesion to the pieces of metal it’s trying to join.
Among Hackaday’s readership will be a few elite-level metalworkers whose welds are works of art.
I may sometimes approach that level of skill with soldering, but when it comes to welding I am not one of them. I suspect I share this with many readers, while I have a basic handle on the job I am still pretty inept. I’ll get the welding current wrong, I’ll sometimes get my arc length wrong, and I’ll move across the work at the wrong speed. Despite that, I will often manage to produce welds with a creditable outward appearance once I’ve knocked off the flux, but which may still conceal fundamental flaws beneath them.
Many people who have received professional instruction on welding will have had their teachers devote countless hours to the pursuit of drawing a perfect bead. It’s an entirely appropriate skill to acquire because repetition teaches those skills of maintaining arc length and cover integrity that are the key to producing consistently good welds, but it shouldn’t lead to the conclusion that it is the bead that’s important rather than those arc skills. An inept welder can produce a surprisingly good-looking bead that conceals a less pretty weld, I should know this because I have done it.
Do You Have Ten Thousand Hours?
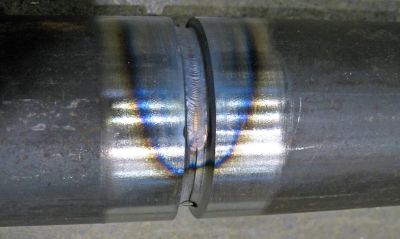
I thus make full use of the angle grinder when I weld, though I don’t always grind my welds as far back as I did with that 1mm tube. The sight of good metal exposed under that bead is the confirmation that the weld is a good one, and if I see any anomalies it’s my cue to take it back all the way and try again. If you take a look again at the tube you’ll see just such a flaw in the join, if it wasn’t simply a test to see whether such a thin piece of stock as possible with that welder I’d be doing it again.
I think professional welders would universally consider this welding gear a toy — as an Easy-bake oven is to a professional baker. So for you pros out there, let’s see those pristine beads, for those weekend welders, by all means, grind them down and show us what they’re really made of.
0 Comments